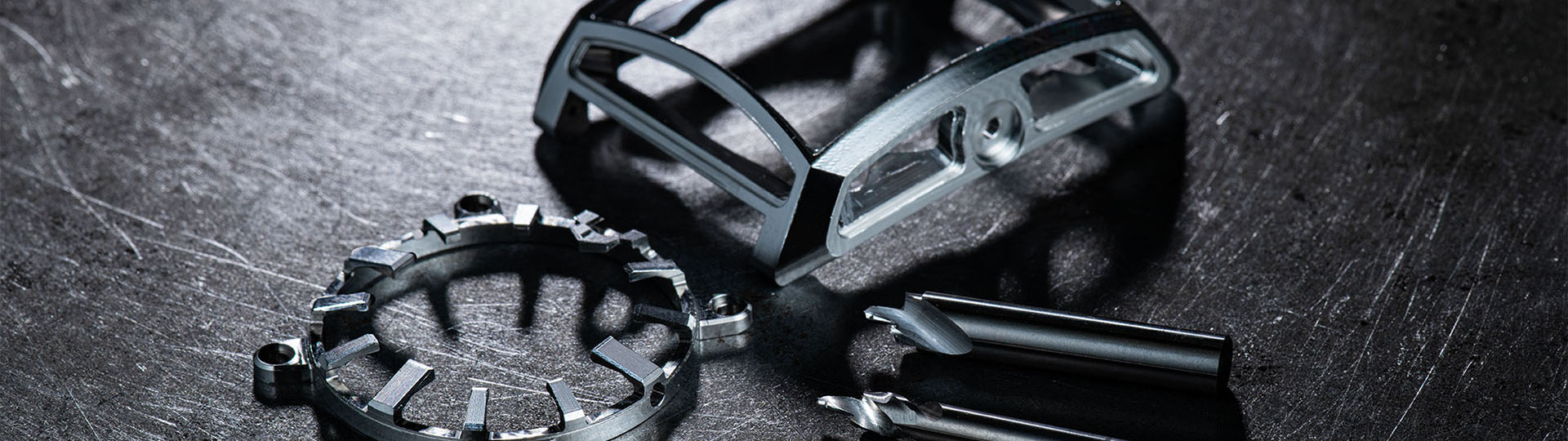
OUR STORY
Pride of a drill manufacturer

The origin of MINASE is drilling tools, which are symbolized in the brand logo.
MINASE is a brand of state-of-the-art watches that have been supremely crafted by KYOWA, a high-performance tool manufacturer that has the cutting and polishing technologies required to bring out the true precision and beauty of metals, involving passion in the ceaseless pursuit of perfection.
The inspiring features of MINASE watches are bold yet intricate.
They feature ultra-three-dimensional designs not even conceived of by other major watch brands the world over. The novel structure of the watches allows their minute cross-sections to be polished more finely than ever before.


MINASE watches are made entirely of hand-crafted components.
Only a technologically outstanding manufacturer can begin to appreciate the idea of making such watches. But even with the technology on hand, watches like MINASE still require dedication and time to attain perfection.
MINASE keeps making its watches to satisfy true aficionados in the world who seek watches with the ultimate industrial design, a sense of presence, modernity, and artistry that can never be imitated by mass-produced watches.

In 2017, the company took its collection of MINASE watches to Switzerland, where the timepiece industry is held in the highest regard, to test its mettle.
Not even in Switzerland is there the precedent of a tool manufacturer involved in watchmaking. But, gazing at these watches, the highly advanced technology that went into making them, along with the story of our unrelenting passion behind the products, are evident.
The watches must have special allure to capture the hearts of so many in Switzerland and the rest of Europe.
Our faith was confirmed: MINASE has won the hearts of watch collectors and become a brand that symbolizes the handmade watches that the world expects to see from Japan.
We are proud of our origin as a drilling tool manufacturer.

Terroir precision

MINASE has its roots in the town of Minase in Akita Prefecture, 600 km north of Tokyo.
Minase is blessed with beautiful conifer forests and pristine rivers, which become covered in deep snow in winter, cutting off the town from the rest of the world. Perhaps it is no coincidence that the town resembles a small Swiss village nestled in the Jura Mountains.
Terroir in watchmaking.
The term is often used in the wine industry to describe the natural environment, climate, and culture of a geographical area in terms of how they affect the unique taste and body of the wines produced there. Applying the concept to watchmaking, the people of Minase have terroir similar to the Jura villagers’ that allows them to ceaselessly devote themselves to such an intricate craft.

Since ancient times, Japanese culture has excelled at forging metals and imparting luster. Indeed, some of the parts used in MINASE watches take a skilled artisan 90 minutes to fully polish.
Why are MINASE’s watchmakers capable of relentlessly pursuing mastery in their craft? What is the source of their dedication? Perhaps it’s driven by the terroir of Minase.

MILESTONE
Global sales start.
Global sales start.