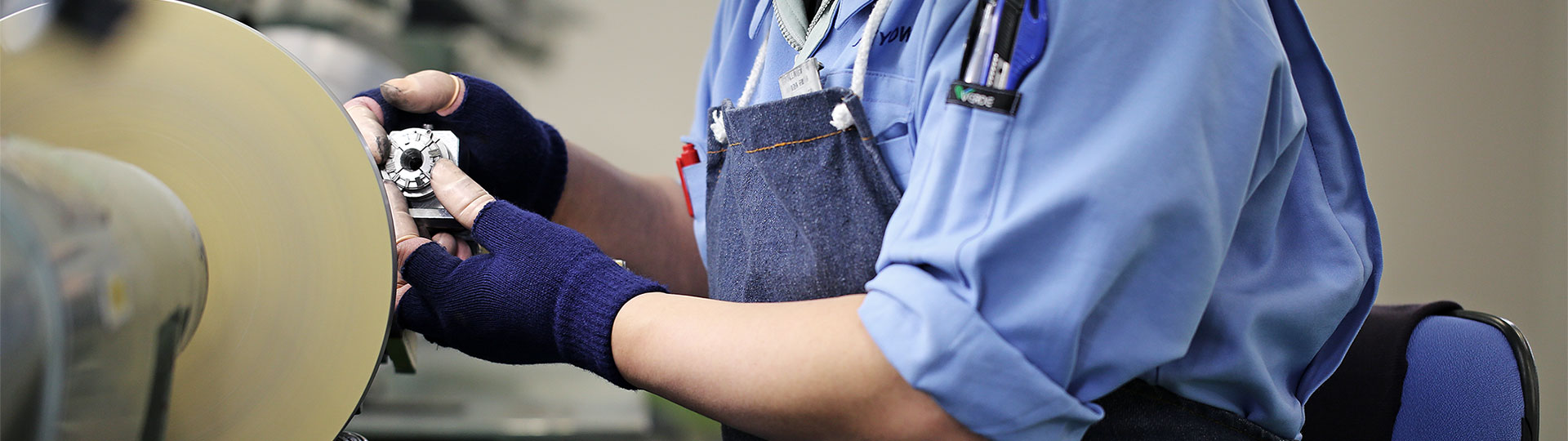
SALLAZ POLISHING
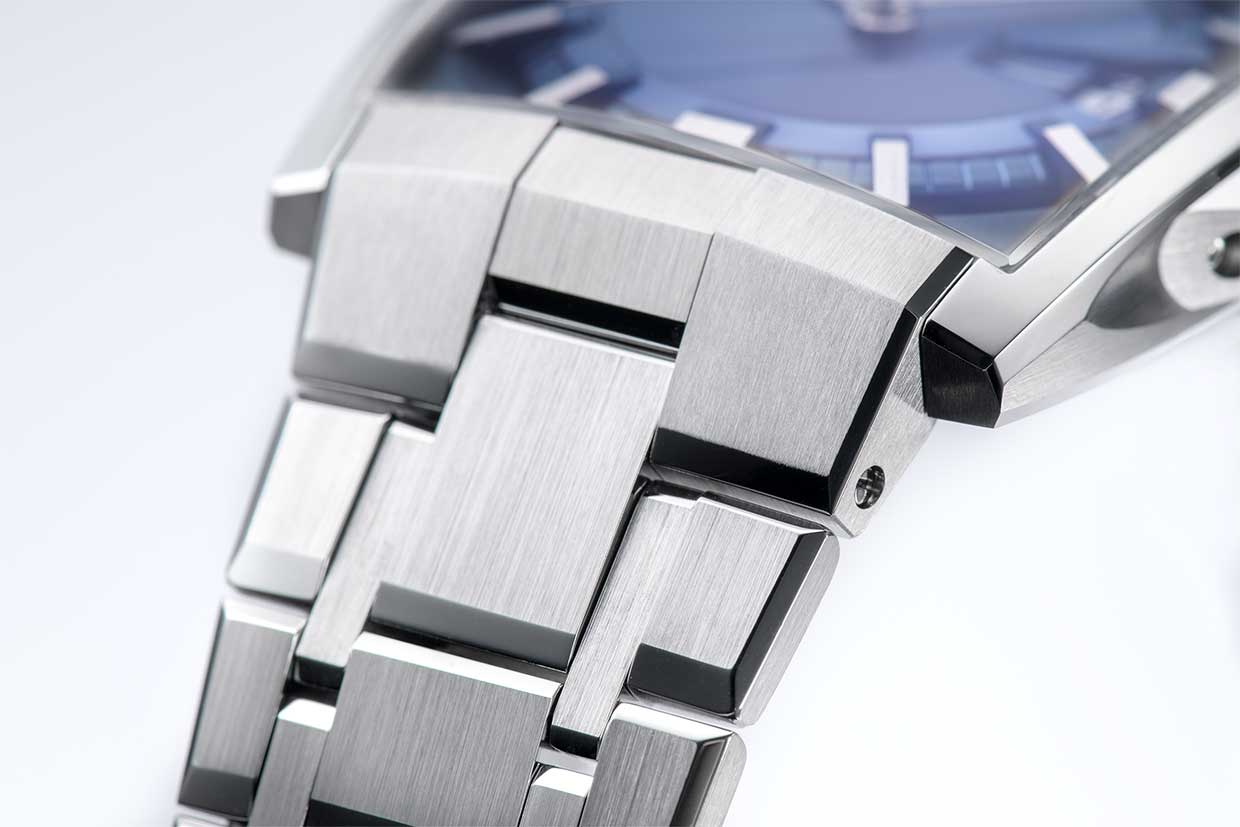
Bringing a shine to all cut surfaces
If you ask any watch collector in the world what comes to mind when they hear the term Sallaz polishing, they are likely to say MINASE. That’s because the brand has become synonymous with the technique used to produce handmade watches.
Sallaz polishing is used to improve the smoothness and uniformity of the bare surfaces of a watch before the finishing touches are applied.
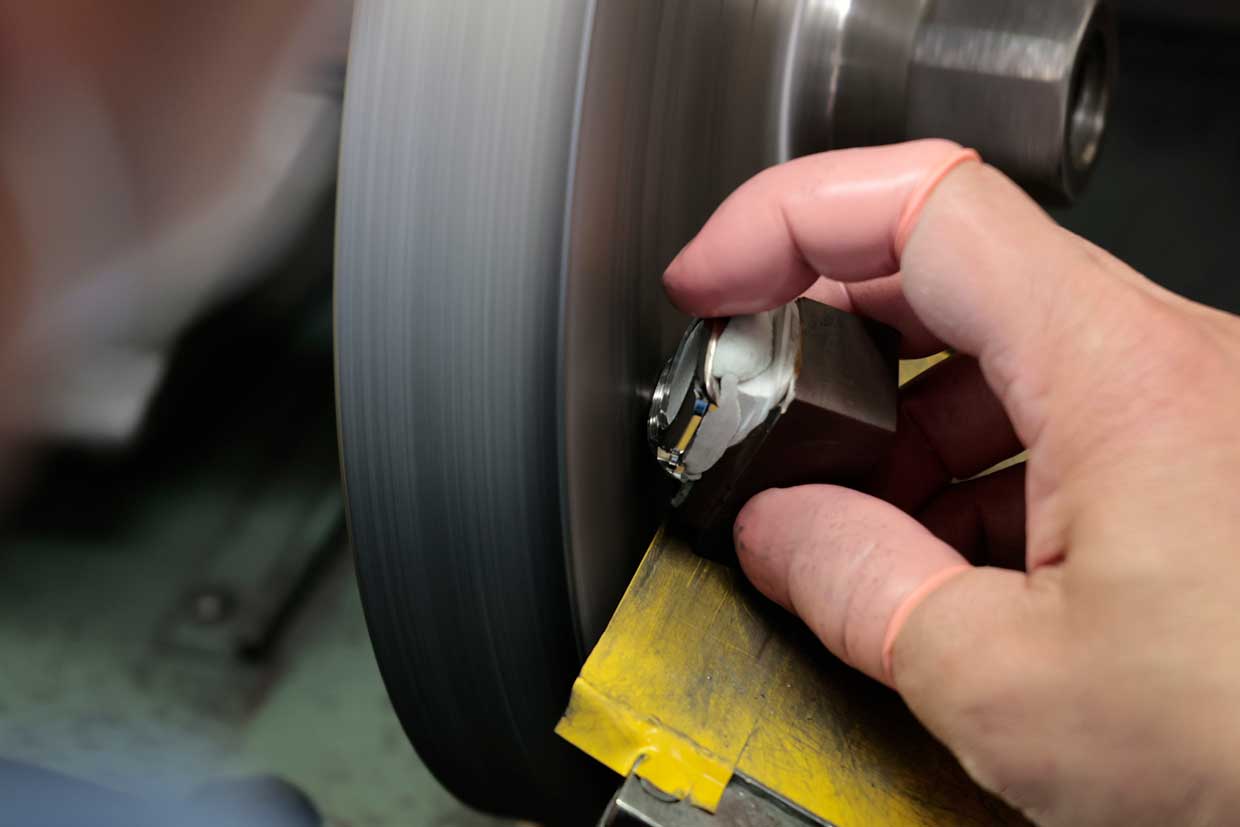
The process entails skilled artisans focusing all their attention on their fingertips as they gently stroke the metal surface, manually polishing every cross section of each part, one by one. This is such meticulous work that it takes even the most seasoned watchmaker up to 90 minutes to polish a single part of a MINASE watch.
So if you come across a MINASE timepiece, please use a magnifying glass like those used at art auctions to observe its finest details. You will see with your own eyes how the myriad cut surfaces of the watch all reflect light brilliantly.
As Sallaz was originally the name of Swiss-made machinery, the technique surely originated there, but appears to have been lost with the passage of time.
Meanwhile, MINASE has adopted and evolved this special technique in its own unique way, in the snow-covered town of Minase in Japan, half a world away from Switzerland.
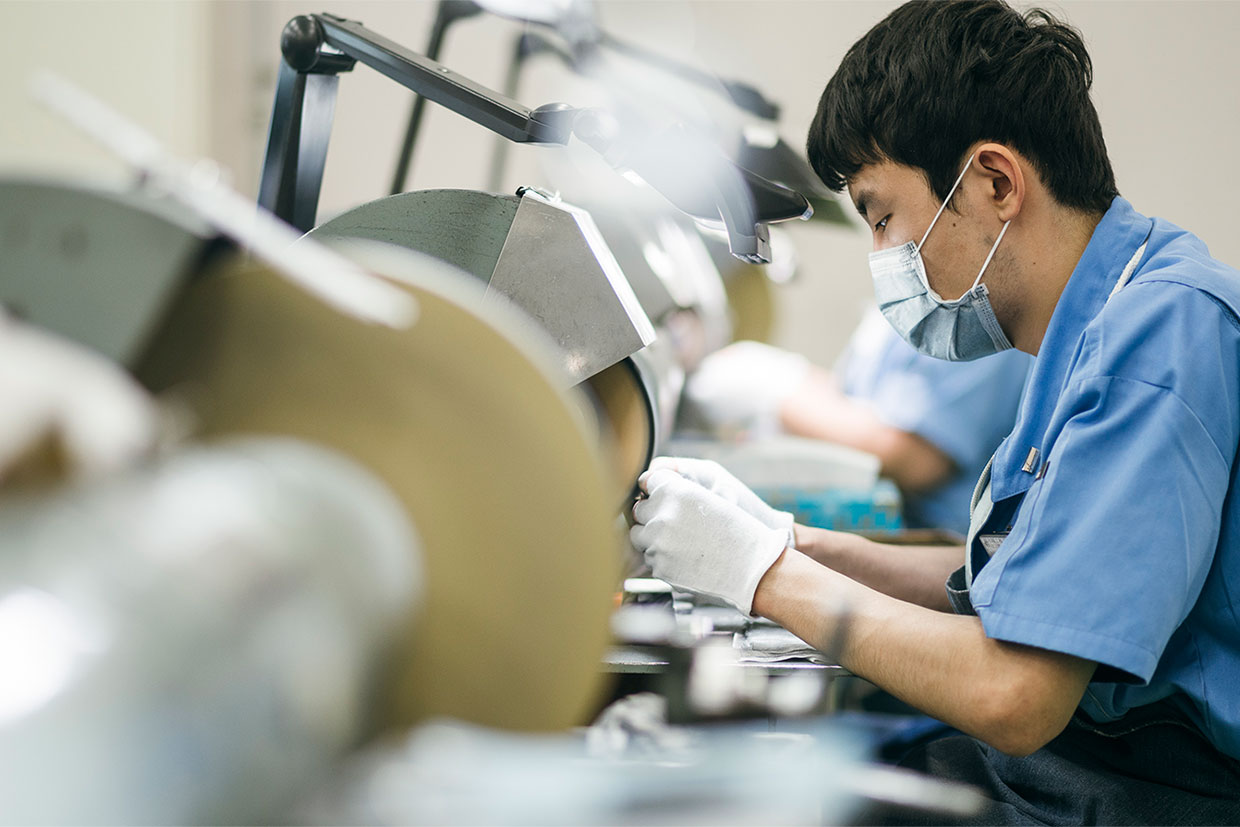
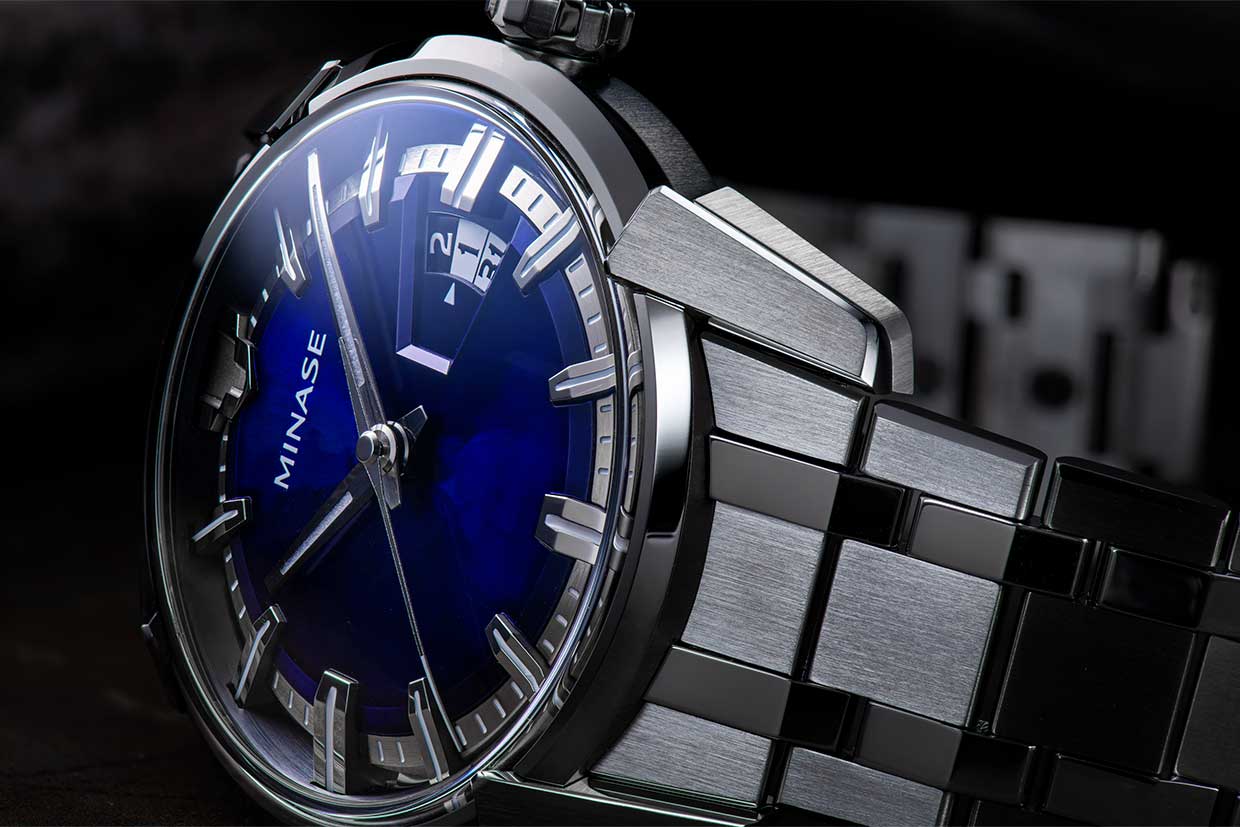
At MINASE, we do not compromise when it comes to creating beauty and making all surfaces of each of our watches shine.
We take as much time and effort as the work requires.
Sallaz polishing is but one of several symbolic elements of MINASE-ISM.